Laser Cut Problems
Hi! It has been a while. Part of that is because progress has been slower than I would like just because I've been busy. The other part is that Van's has seen some quality control issues with their laser cut parts and I may have to now dissemble things to replace spars depending on how that goes. That isn't ideal and it is a real motivation killer (not to mention it is really frustrating). Here is the email I got from Van's on the issue:
Dear Van’s RV Kit Builder,
We’re writing to inform you about an issue that’s been reported to us by some RV builders. We are in the process of reviewing the situation and want to share what we know so far. This email is being sent to those who received a kit which may include one or more laser cut parts.
In early 2022, Van’s began manufacturing some RV kit parts via partner contractors utilizing a fiber laser cutting process. This decision was made after completing a formal manufacturing process evaluation and extensive fatigue testing of laser-cut materials used in the manufacturing process, with the purpose of increasing the production capacity for some parts during a period of high demand.
Van’s has recently received reports from some RV builders of cracks that have occasionally formed in the edges of holes on some laser-cut parts either while dimpling or while riveting the dimpled holes. The frequency and consistency of reported cracks has been variable, as some customers have experienced cracking while others have not. We are acting on these reports by investing time, resources, and energy to investigating the customer-reported concerns, conducting extensive tests on parts and materials, and providing answers to questions.
We will communicate more information updates as time goes on. We will post updates and details to our web site at least weekly (available at this link) as new information becomes available. We appreciate your patience as we work through the various details.
A few things we want you to know:
We are communicating with you now because our records indicate you may have received laser-cut parts in your kit(s), based on your specific kit shipment date(s) and the timeframes in which the applicable laser-cut parts were available to be shipped to customers.
All of the parts that were manufactured beginning in 2022 utilizing the laser cutting process are now being produced on CNC punch press machines, as they were before. A smaller number of non-dimpled or non-structural parts that have always been laser cut are still being manufactured that way.
We are conducting extensive testing of parts and materials. These tests are being performed both at Van’s and at an internationally recognized company that specializes in these types of tests. The results of these tests, which are comprehensive and redundant in nature, will be communicated as the data is received and analyzed.
Crated kits that were packed prior to the manufacturing change that are already at shipping warehouse facilities, etc. may contain laser-cut parts, and we will work with customers who receive those parts.
Van’s will replace any laser-cut parts which are dimpled by the builder during the construction process, upon request, as soon as we are able to do so based on parts availability. We will provide information about availability of replacement parts, as well as a formal process for requesting replacement parts, as we develop and confirm our plans for manufacturing. Note that not all parts are in stock at this time, regardless of the availability status displayed on our online store. Our online store inventory status will be updated soon to reflect the removal of laser-cut part counts from our inventory. Please do not place an online store order or a call-in order for parts at this time, as we need to establish a standard process to help ensure we can serve each customer smoothly. We will communicate the details of that process as soon as it is ready to go.
The team at Van’s will do our best to provide replacement parts as soon as possible. Creating replacement parts will take time. We are prioritizing the manufacturing of parts on our CNC punch presses, as well as providing tooling to our partner punch press contractors. It will take a number of weeks before that tooling arrives and can be put to use. We will ramp up production as quickly as possible within the necessary constraints of tooling readiness and strict quality control.
Quick Build kits are inspected at Van’s prior to shipping. Should any issues be observed by a customer, they should contact Van’s and we will work with them to assess and address concerns as needed. We will communicate directly with these customers regarding a process to follow, as well.
Additional testing and evaluation we are currently performing:
We are conducting extensive tests of parts with holes containing cracks and notches, because cracks could potentially be present in holes that make it into the field. Therefore, we need to understand the real-world impact: how and when cracks form, how and whether cracks may propagate, and what the actual results of any propagation might be. Initial testing indicated that laser-cut parts had a lifespan very close to that of punched parts (and well beyond the expected necessary lifespan of an airplane). Additional testing is being conducted now by Van’s as well as a contracted third-party testing partner. The results of these tests will provide additional valuable information and will also serve in the review of prior test results.
Currently, the parts of greatest potential concern are the following laser-cut parts:
Vertical stabilizer, rudder, and elevator spars on all RV-7, RV-8, RV-9, RV-10, and RV-14 empennage/tail kits;
Horizontal stabilizer spars in RV-7/8 empennage kits;
Some flap and aileron spars that were shipped early in the laser-cutting process, in RV-7, RV-8, RV-9, RV-10, and RV-14 kits
We encourage people to pause building of the above specific kits that include laser-cut empennage/tail, aileron, and flap spar parts. We will be replacing these components and providing further guidance. Even though testing of these specific parts is not yet complete, Van’s is erring on the side of caution by identifying those parts now and will recommend the replacement of these parts due to the relatively high loads carried by those specific parts. We are executing an initial run of replacement parts on our punch presses now and will be making additional production runs.
Our testing program for this issue is ongoing and is focused on reviewing the various hole diameters and material thicknesses/types that are used to produce the affected aircraft parts. These variables, as well as variations in manufacturing process parameters, may result in a marked difference in the potential for a crack to form and propagate in a given hole. We will prioritize testing and manufacturing of replacement parts based on these differences. We are also reviewing the metallurgy of the holes at the third-party test lab, in order to better understand the origin and cause of observed cracks, and effect on the performance (and lifespan, if applicable) of the part. From that, we will gain a greater understanding about these cracks and at what stages in the process they are formed (when cut, when dimpled, when riveted). We expect to receive those results soon, even before the full spectrum of overall testing is completed, and we will communicate that information when available.
Extensive fatigue testing is underway and will take some time to complete, due to the length of each test and the exhaustive number of tests being performed. Tests are being conducted at multiple locations. It will take time to build a comprehensive sample size that will yield results with the highest level of confidence. Van’s and our contract test partner are working around the clock on this process.
We have published a list of affected parts (which is available at this link) and have classified each part to indicate the current status of each. We will update that list based on test results as they are received. This list and the associated status of each part will determine the order in which we will produce replacement parts (higher-priority parts will be manufactured first). We plan to execute multiple smaller manufacturing runs of parts from the priority list, as compared to our typical large batch runs.
Please understand that the team at Van’s is hard at work on this and that our priority is making sure these issues are carefully, accurately, and thoughtfully reviewed and addressed. We will communicate new information as it becomes available. We understand that builders want and need answers as soon as possible, and we will provide updates to you as well as our teams internally as soon as we have information. Note that questions asked of our team before we have full information in hand will necessarily have to be answered with something similar to, “That information is pending, and we’re working hard to get it to you as soon as possible.” We hope you’ll understand that, and please know that we will communicate proactively as new information becomes available.
We are working for you to provide quality parts and service. We understand this is frustrating for affected customers and want you to know that we are here, we are listening, and we will work to make things right.
Again, we plan to update you with new information when we have it.
Thank you for your understanding, patience and support.
And my opinion on all that? It sucks. I want to have faith that the airplane I am building will, you know, stay in the air and not kill me. Now I have to go back through and reinspect everything and potentially undo pretty much any and all work I've accomplished. Once that is done, getting replacements will mean all those have to be prepared again and it is just... a lot. I'm going to sit on my thoughts about this for a while and then go inventory my parts to see what I have.
So, what progress did I actually make? I got some rudder parts painted and put together.
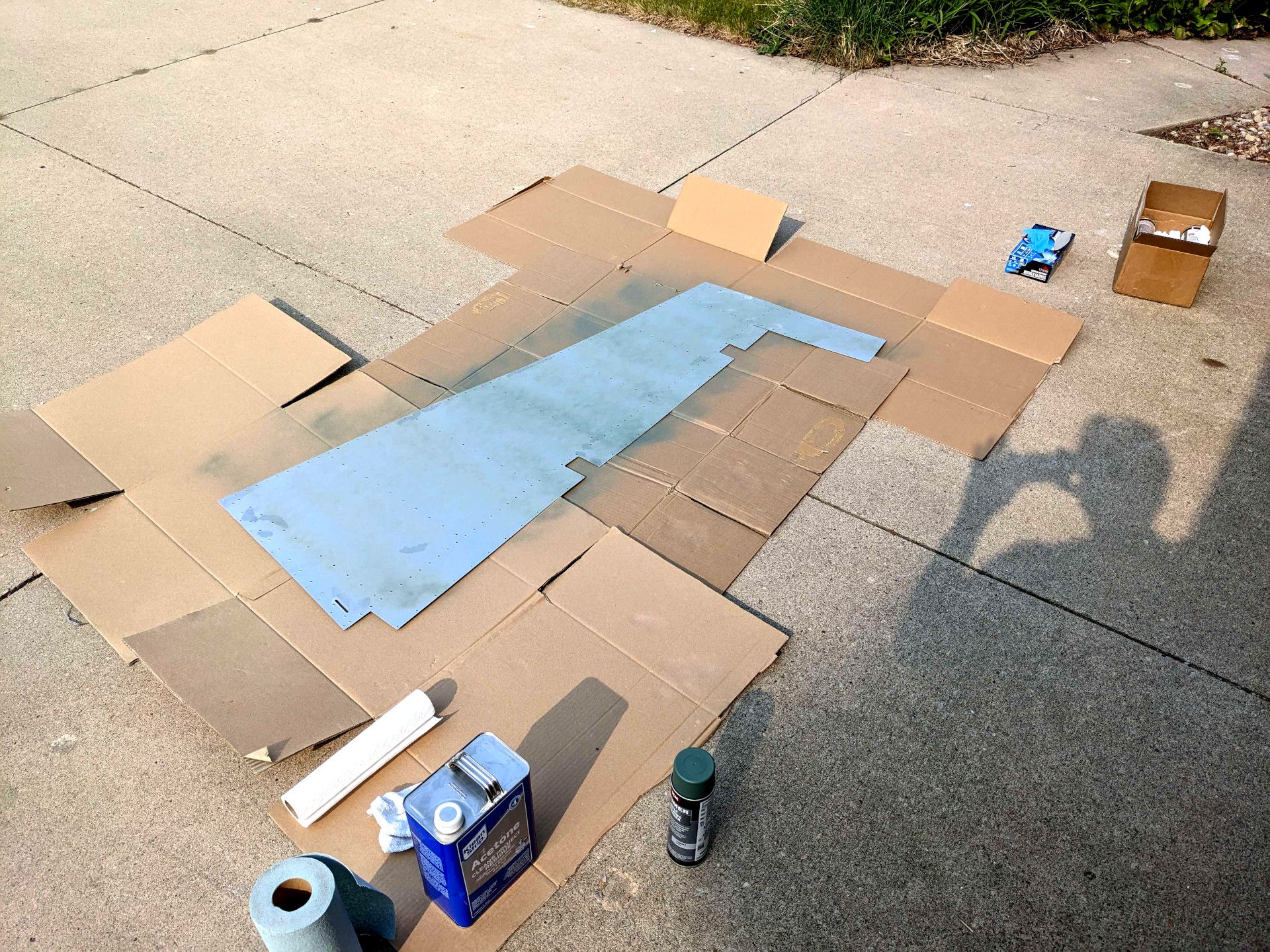
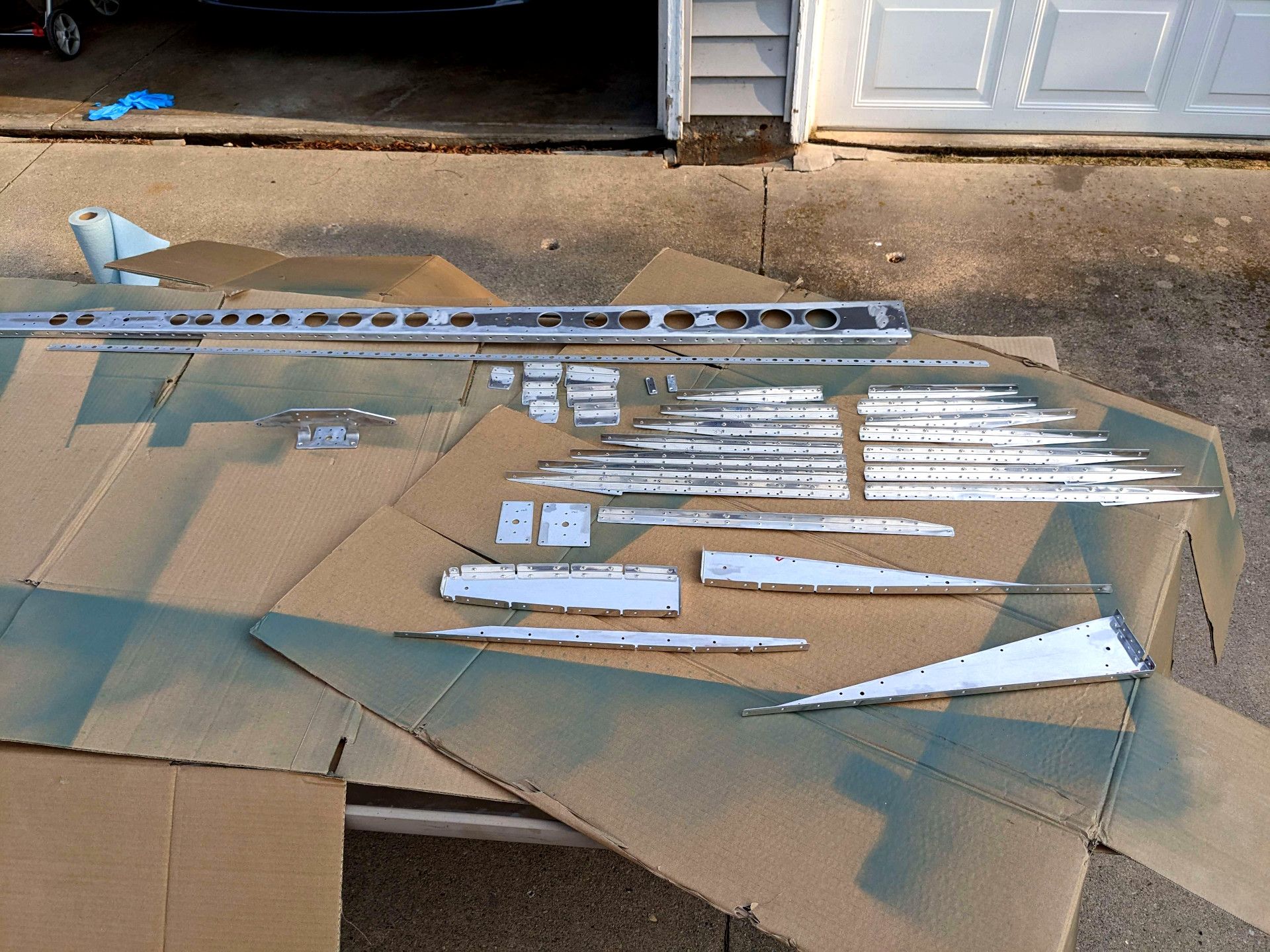


but some of the keen eye'd among you might notice that I didn't scuff the surface well so the primer isn't really staying on the best. That's on me for being impatient. Painting outside was a nice change of pace though. I do recommend that. But anyway, the show must go on and go on it did. I riveted the stiffeners to the rudder skin.

I also riveted the reinforcement doublers to the main rudder spar with the nutplates.

and moving right along, I riveted the rudder horn to the bottom rib of the rudder.

Some time during all this my replacement skin arrived from when I messed up the other skin. So I prepared it and dimpled it (more carefully) and then scuffed it for painting. The resulting image looks cool.
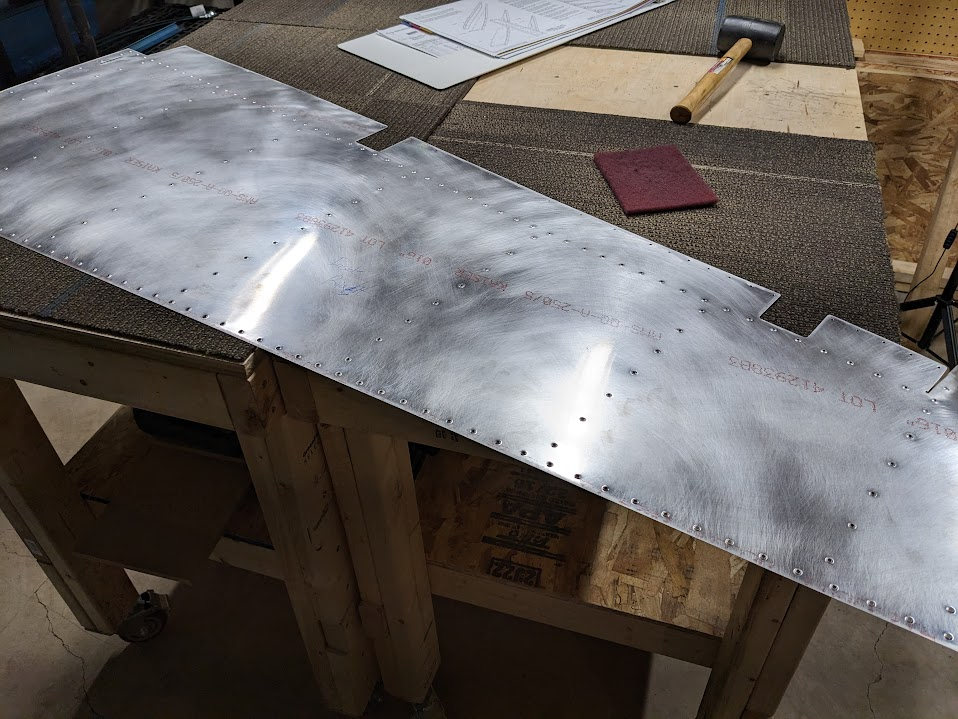
Once the second skin was painted, I attached the stiffeners and the rudder horn (expect for the rivets at the very end for reasons that will become apparent here in a moment)

and then I hit a snag that took me a few hours to resolve. How on earth was I going to buck or squeeze the rivet on the very end? This is how the instructions recommend doing it and yet you end up with no space at all!
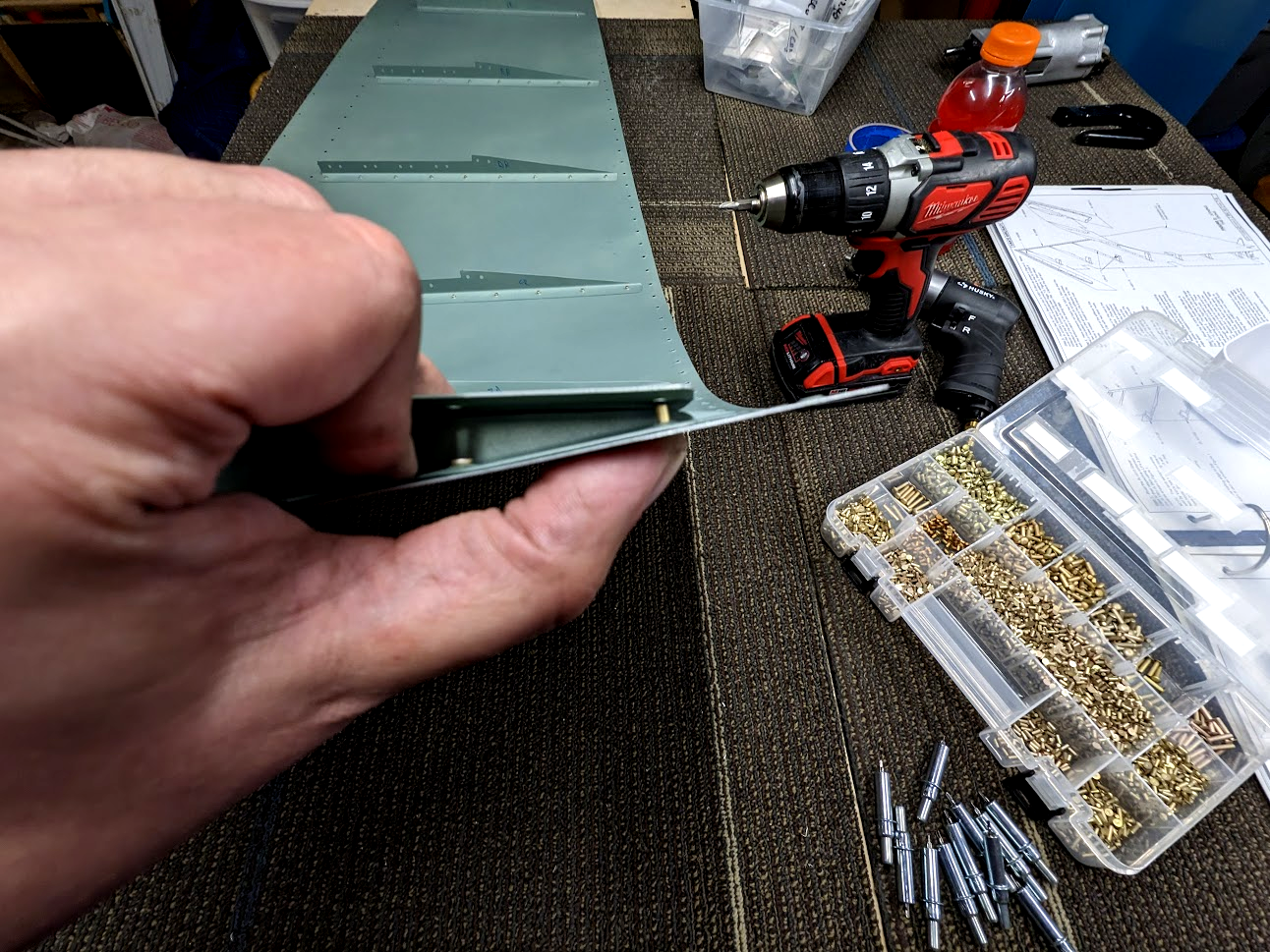
So I tried offset riveting, some other crazy things, put in a blind rivet (but the tail was too long so I removed it), cried a bit, invented new curse words... then I went online to see what other people had done and if I could just copy that. Other people's experience is a great tool and I found a few options. The easiest seemed to be just drilling out a few rivets of the bottom rib so that one could get access to rivet. So I did just that.


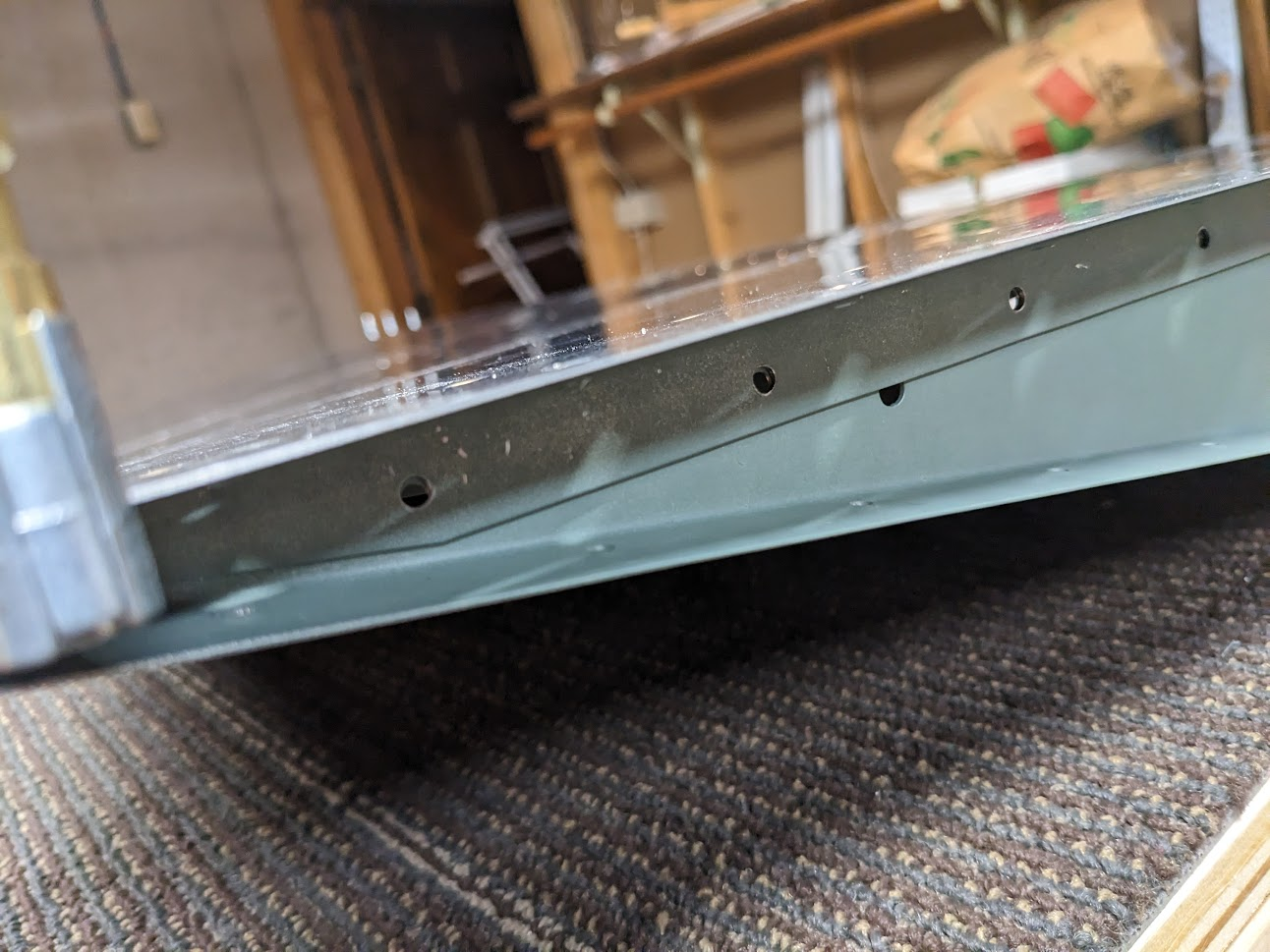

It wasn't that hard to do but it is a real put off when you are following instructions and then run into something like that without so much as a heads up. The clips for the rivet stiffeners just use blind rivets and are easy enough to do.
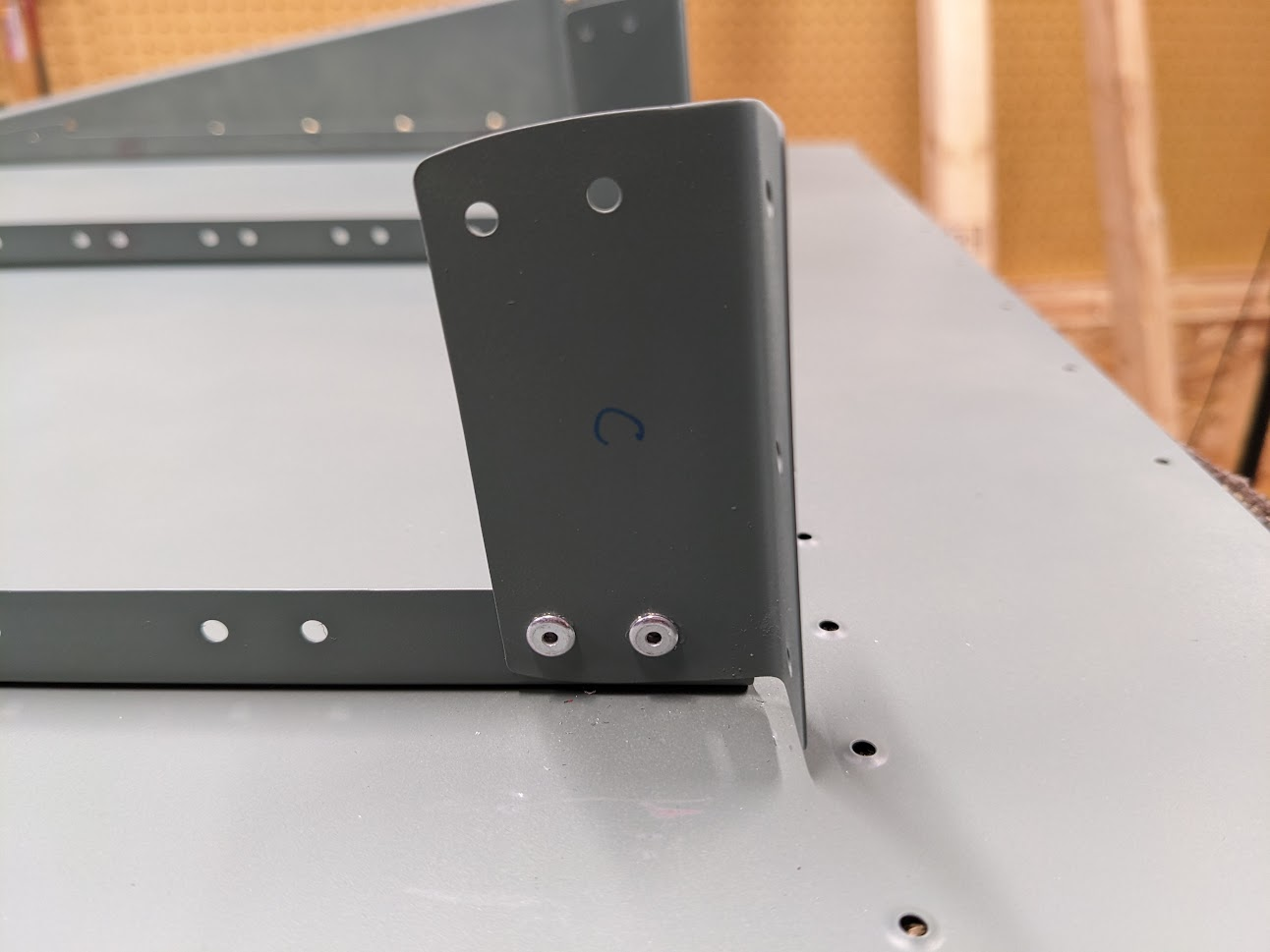

As a gentle reminder, sometimes I stream the work I'm doing on twitch! So I don't have pictures of that work because my phone is also my camera. But I did some counter-sink work of the trailing edge (because I forgot) and was just about to attach it all together. That's where the work is hanging right now.
So I am unsure what my next steps are. I am trying to figure out how much I need to inspect or take to pieces and what parts I have that are suspect in my inventory. On the plus side, EAA is next week and I've done some more flying.
Here are a slew of photos of me just enjoying flying. I chased some boats, found a bunch of boats anchored by some islands and people just partying, and just enjoyed the freedom that is flying!
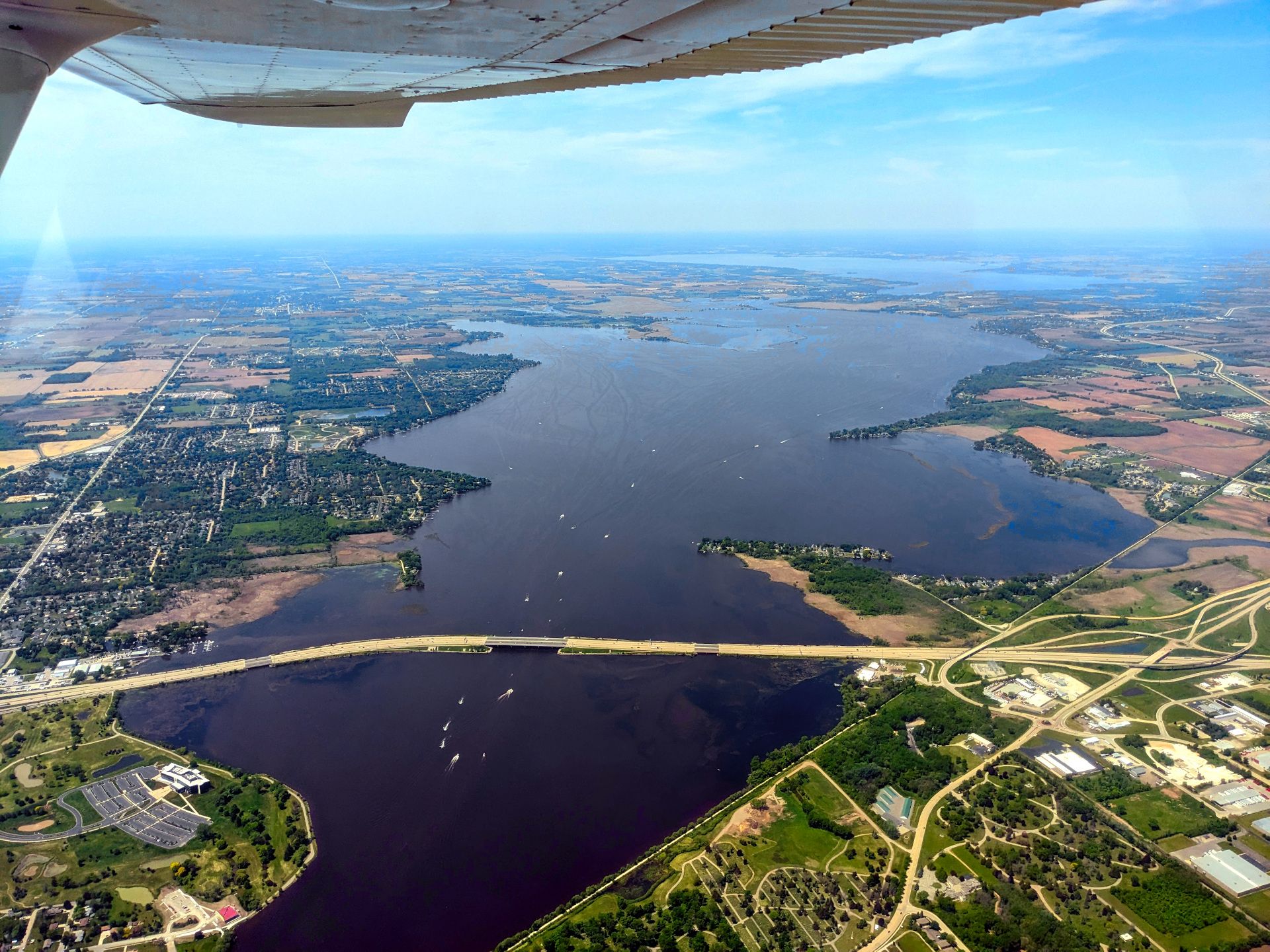
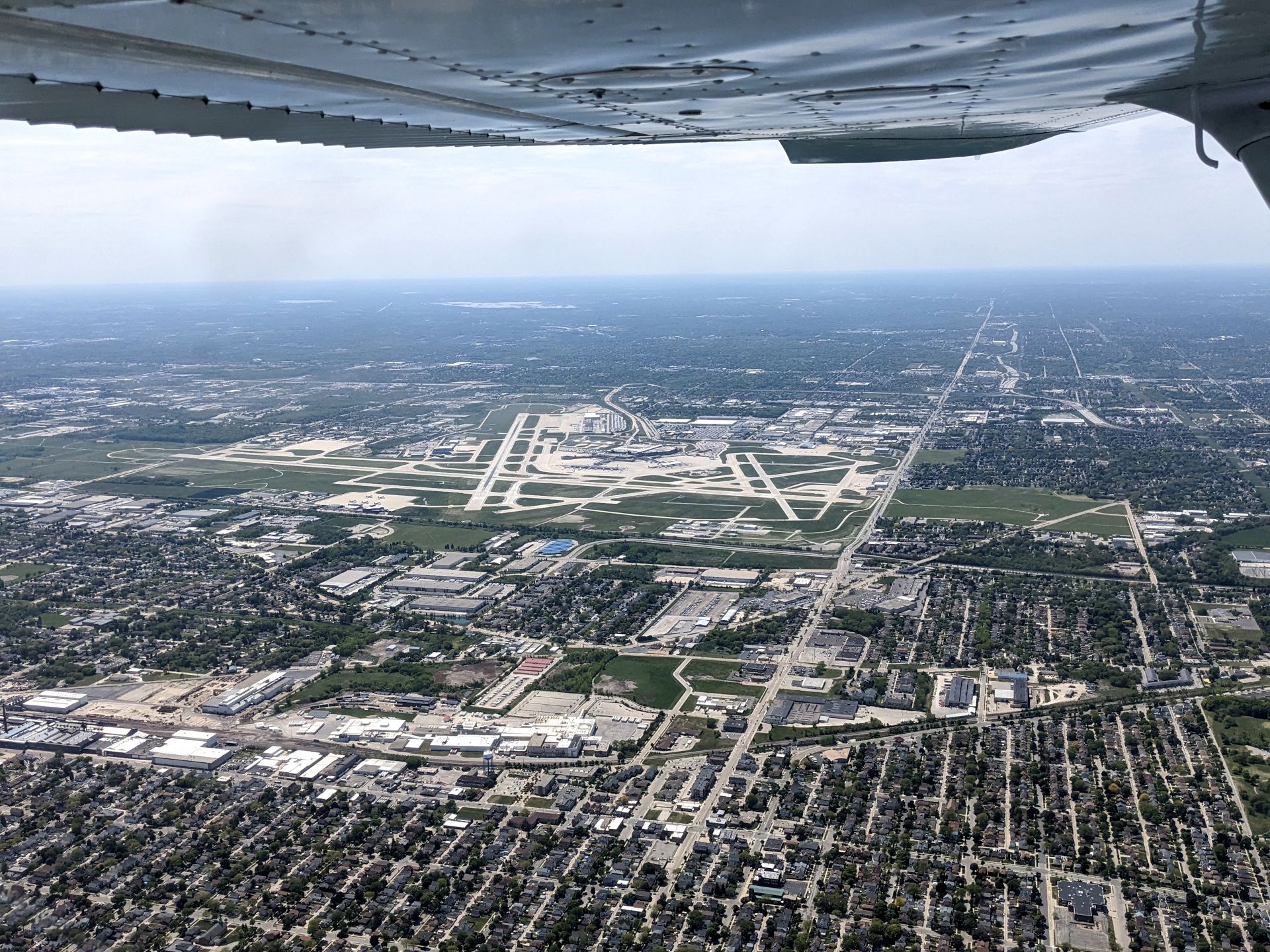

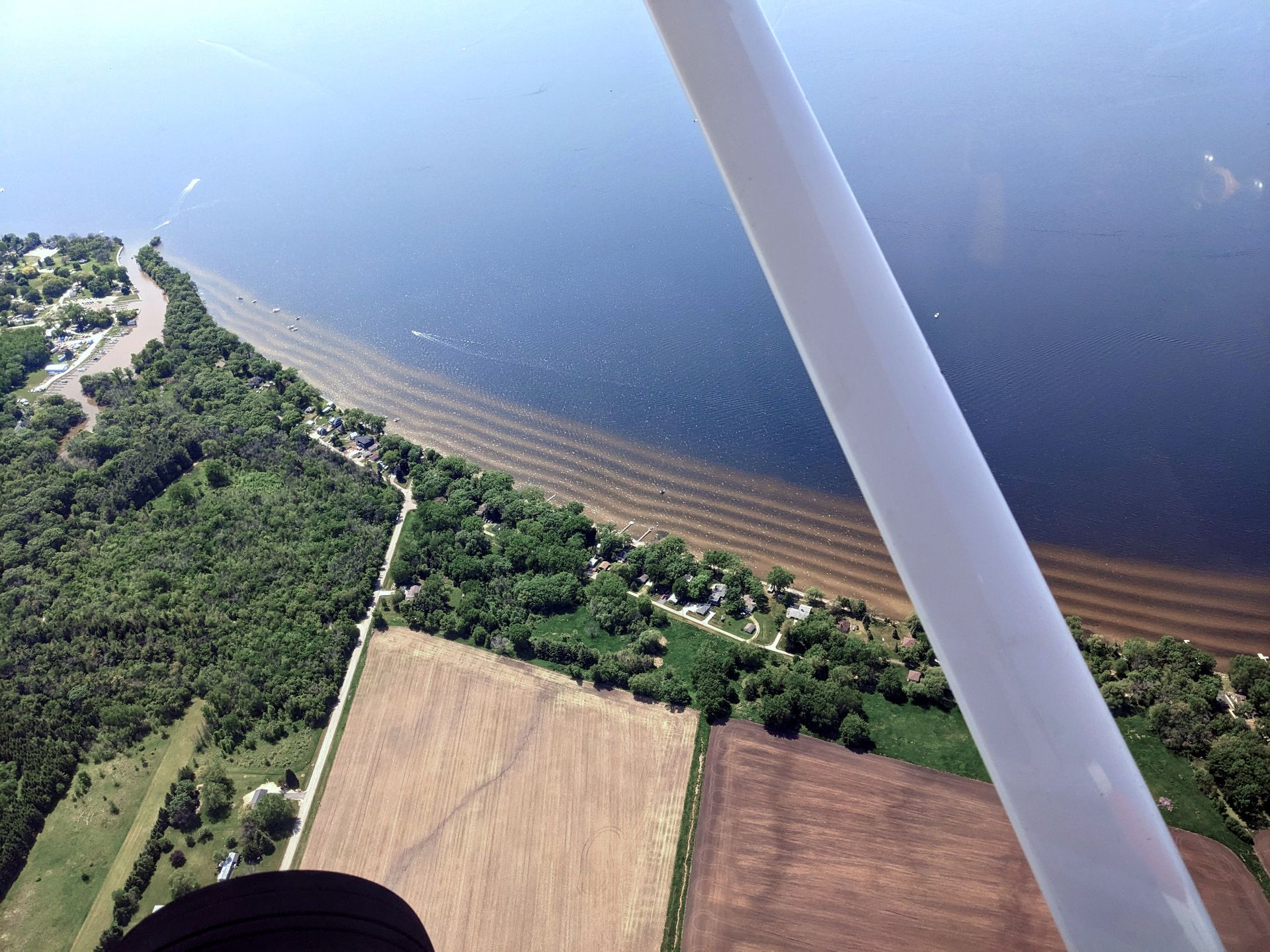



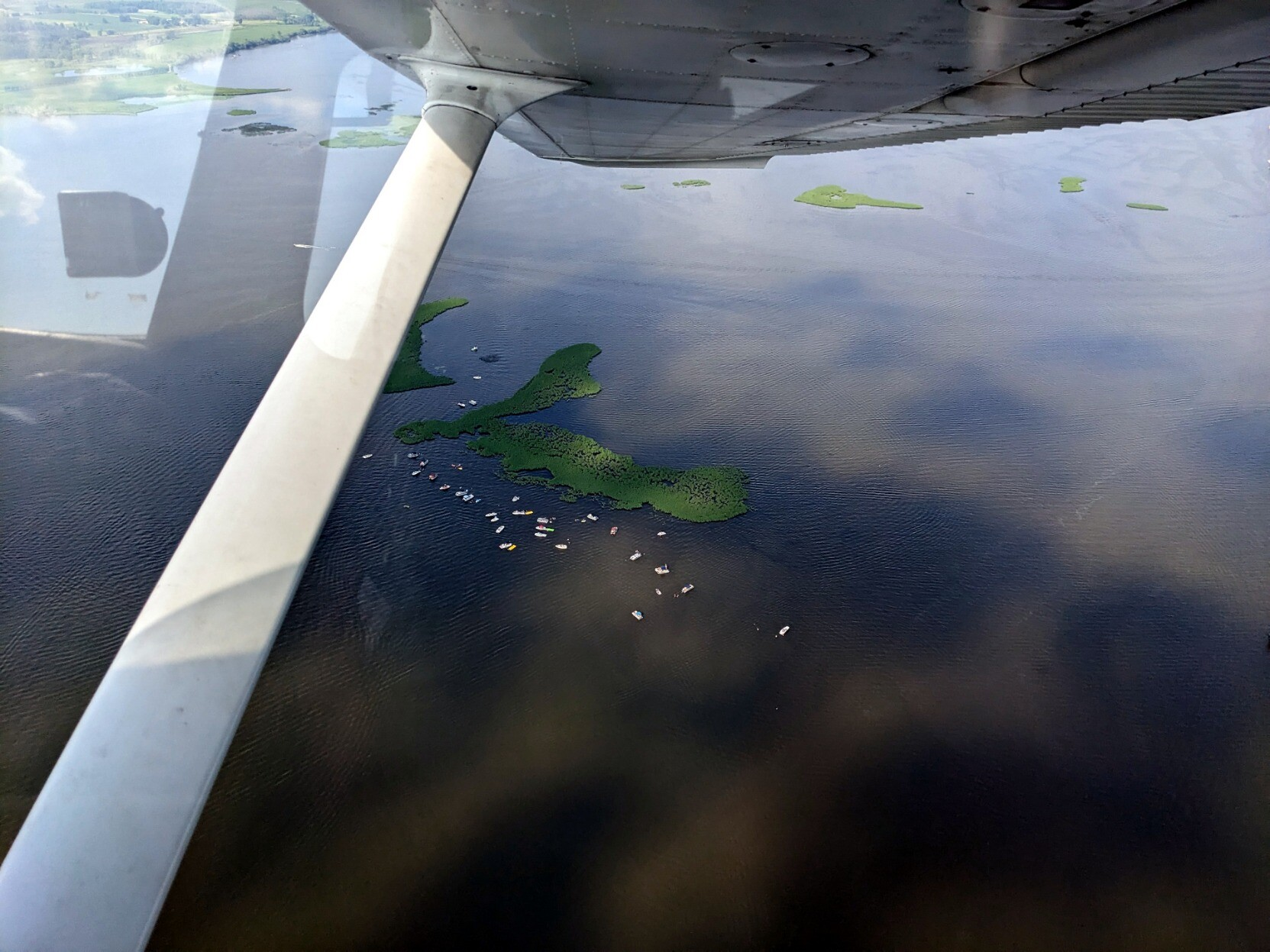
Thanks for coming by! Sorry I don't update super regularly but in news that is apparently only a surprise to me, holidays, having a family, and having other projects can take up a lot of time! If only I could just be independently wealthy! Oh well, not today. I hope to take a lot of photos and do a lot of things at the EAA Air Venture fly in next week. I might even see some of you there!